Business & Management
NEIoT Higher Apprenticeship
Level 5 Operations / Departmental Manager Higher Apprenticeship
Overview
An Operations or departmental manager is someone who manages teams and/or projects, and achieving operational or departmental goals and objectives, as part of the delivery of the organisations strategy. They are accountable to a more senior manager or business owner. Working in the private, public or third sector and in all sizes of organisation, specific responsibilities and job titles will vary, but the knowledge, skills and behaviours needed will be the same. Key responsibilities may include creating and delivering operational plans, managing projects, leading and managing teams, managing change, financial and resource management, talent management, coaching and mentoring. Roles may include: Operations manager, Regional manager, Divisional manager, Department manager and Specialist managers.
Key responsibilities are likely to include supporting, managing and developing team members, managing projects, planning and monitoring workloads and resources, delivering operational plans, resolving problems, and building relationships internally and externally.
Work includes manufacturing bridges, oil rigs, ships, petro-chemical installations, cranes, platforms, aircraft, automotive and machinery parts, sheet metal enclosures, equipment supports, and anything that can be fabricated out of metal. Fabricators can work alone or in teams, in factories or on operational sites. Fabricators use a large range of metals including steel, aluminium and titanium at a range of thicknesses from 0.5mm up to over 20mm. The size and weight of the fabrications can range from components that can easily be picked up by hand, to massive structures that require several cranes to manipulate.
In their daily work, an employee in this occupation interacts with planners, supervisors, inspectors, designers, welders, pipefitters, fitters, machinists, riggers, steel erectors, stores personnel, painters and many others involved in manufacturing, production, maintenance and repair.
An employee in this occupation will be responsible for the quality and accuracy of their own work whilst ensuring it conforms to a relevant specification such as an engineering drawing or an international standard. Fabricators are also responsible for the health, safety and environmental (HS&E) protection of themselves and others around them.
Engineering Technicians in the Automotive and wider Advanced Manufacturing and Engineering Sector are predominantly involved in highly skilled, complex work and must, as a minimum be able to:
Apply safe systems of working
Make a technical contribution to either the design, development, quality assurance, manufacture, installation, commissioning, decommissioning, operation or maintenance of products, equipment, systems, processes or services
Apply proven techniques and procedures to solve engineering/manufacturing problems
Demonstrate effective interpersonal skills in communicating both technical and non-technical information
Have a commitment to continued professional development
Engineering Technicians take responsibility for the quality and accuracy of the work they undertake within the limits of their personal authority. They also need to be able to demonstrate a core set of behaviours in order to be competent in their job role, complement wider business strategy and development. This will enable them to support their long term career development.
Engineered and manufactured products and systems that Engineering Technicians work on could involve mechanical, electrical, electronic, electromechanical and fluid power components/systems.
Organisational performance – delivering results
Interpersonal excellence – managing people and developing relationships
Personal effectiveness – managing self
Organisational performance – delivering results
Interpersonal excellence – managing people and developing relationships
Personal effectiveness – managing self
Organisational performance - delivering results
Personal effectiveness – managing self
Interpersonal excellence – managing people and developing relationships
Organisational performance – delivering results
Personal effectiveness – managing self
The importance of complying with statutory, quality, organisational and health and safety regulations
General engineering mathematical and scientific principles, methods, techniques, graphical expressions, symbols formulae and calculations
The structure, properties and characteristics of common materials
The typical problems that may arise within their normal work activities/environment
Approved diagnostic methods and techniques used to help solve engineering problems
The importance of only using current approved processes, procedures, documentation and the potential implications if they are not adhered to
The different roles and functions in the organisation and how they interact
Why it is important to continually review fabrication and general engineering processes and procedures
The correct methods of moving and handling materials
Processes for preparing materials to be marked out
The tools and techniques available for cutting, shaping, assembling and finishing materials.
Allowances for cutting, notching, bending, rolling and forming materials
Describe Pattern development processes, tooling and equipment
Describe Cutting and forming techniques, tooling and equipment
Describe Assembly and finishing processes, tooling and equipment
Inspection techniques that can be applied to check shape and dimensional accuracy
Factors influencing selection of forming process
Principles, procedures and testing of different joining techniques (Mechanised or Manual)
Equipment associated with Manual or Mechanised joining techniques including maintaining equipment in a reliable and safe condition
Consumables used in Manual or Mechanised joining
Effects of heating and cooling metals
Metallurgy associated with joining
Different types of Welds and joints
How to interpret relevant engineering data and documentation
Skills
Work safely at all times, comply with health & safety legislation, regulations and organisational requirements
Comply with environmental legislation, regulations and organisational requirements
Obtain, check and use the appropriate documentation (such as job instructions, drawings, quality control documentation)Carry out relevant planning and preparation activities before commencing work activity
Undertake the work activity using the correct processes, procedures and equipment
Carry out the required checks (such as quality, compliance or testing) using the correct procedures, processes and/or equipment
Deal promptly and effectively with problems within the limits of their responsibility using approved diagnostic methods and techniques and report those which cannot be resolved to the appropriate personnel
Complete any required documentation using the defined recording systems at the appropriate stages of the work activity
Restore the work area on completion of the activity and where applicable return any resources and consumables to the appropriate location
Identify and follow correct Metal work instructions, specifications, drawing etc.
Mark out using appropriate tools and techniques
Cut and form Metal for the production of fabricated products
Produce and assemble Metal products to required specification and quality requirements
Identify and follow correct joining instructions, specifications, drawing etc.
Carry out the relevant preparation before starting the joining fabrication activity
Set up, check, adjust and use joining and related equipment
Weld joints in accordance with approved welding procedures and quality requirements
understanding the importance of complying with statutory, quality, organisational and health and safety regulations
understanding of general engineering/manufacturing mathematical and scientific principles, methods, techniques, graphical expressions, symbols formulae and calculations used by engineering technicians
understanding the structure, properties and characteristics of common materials used in the sector
understanding the typical problems that may arise within their normal work activities/environment
understanding approved diagnostic methods and techniques used to help solve engineering/manufacturing problems
understanding the importance of only using current approved processes, procedures, documentation and the potential implications for the organisation if this is not adhered to
understanding and interpreting relevant engineering/manufacturing data and documentation in order to complete their job role
understanding the different roles and functions in the organisation and how they interact.
understanding why it is important for an organisation to continually review their processes and procedures
Skills:
obtaining, checking and using the appropriate documentation (such as job instructions, drawings, quality control documentation)
working safely at all times, complying with health, safety and environmental legislation, regulations and organisational requirements
planning and where applicable obtaining all the resources required to undertake the work activity
undertaking the work activity using the correct processes, procedures and equipment
carrying out the required checks (such as quality, compliance or testing) using the correct procedures, processes and/or equipment
dealing promptly and effectively with engineering/manufacturing problems within the limits of their responsibility using approved diagnostic methods and techniques and report those which cannot be resolved to the appropriate personnel
completing any required documentation using the defined recording systems at the appropriate stages of the work activity
restoring the work area on completion of the activity and where applicable return any resources and consumables to the appropriate location
Engineering Design
Engineering Maths
Engineering Science
Managing a Professional Engineering Project
Mechanical Principles
Fundamentals of Thermodynamics and Heat Engines
Optional Units, select two from:
Mechanical Workshop Practices
CAD for Maintenance Engineers
Maintenance Engineering
Production Engineering for Manufacture
On completion, apprentices can register as full members with the Chartered management institute and/or the Institute of leadership and management, and those with 3 years’ of management experience can apply for Chartered manager status through the CMI.
Delivery Sites:
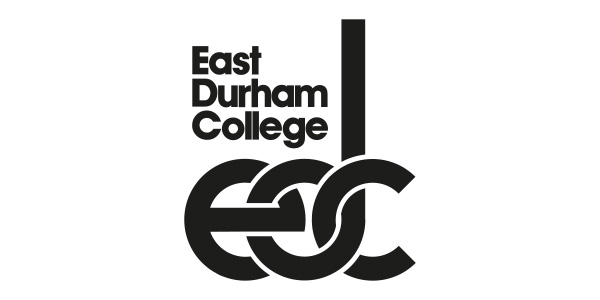